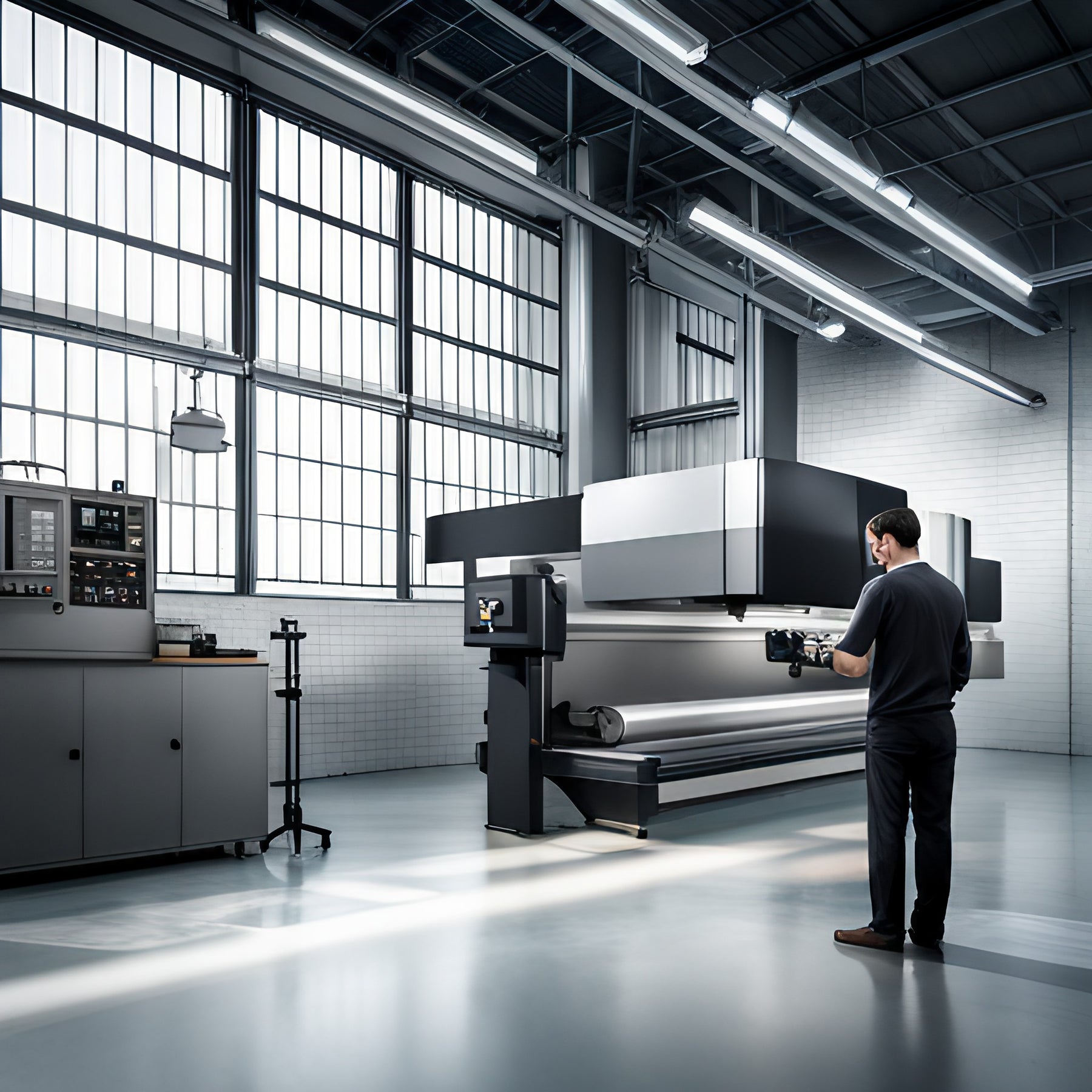
Glossary of CNC Machining Industry Terminology
CNC (Computer Numerical Control) technology refers to the automation of machine tools through the use of computer programs and software. In manufacturing, CNC greatly increases precision, efficiency, and repeatability, reducing the reliance on manual machining processes.
This glossary provides definitions and explanations for key terms and concepts in the CNC industry, catering to both beginners and professionals.
CNC Technology, Processes, and Importance in Manufacturing
CNC Technology: The integration of computer programming and digital control systems to direct and automate machine tools. CNC technology ensures consistent and precise manufacturing of components with tight tolerances, complex geometries, and high-quality finishes.
CNC Processes: A series of programmed steps that guide CNC machines in manufacturing operations. These processes include selecting appropriate tools, generating toolpaths, setting machine parameters, and defining work coordinates.
CNC Metrology and Inspection tools: CNC metrology and inspection tools play a crucial role in ensuring the precision and accuracy of components produced through Computer Numerical Control (CNC) machining processes. These tools are designed to measure and evaluate the dimensional and geometric attributes of machined parts, ensuring compliance with specified tolerances and quality standards. Common CNC metrology tools include CNC calipers, CNC height gauges, CNC Micrometers, Magnetic Base Arm Lengths, CNC indicators tools, CNC parallels tools, CNC Bore Gauges, CNC V Blocks, CNC Gauge Blocks, and CNC hardness testers.
Tooling
Toolholders
Toolholder: A device used to secure the cutting tool in a CNC machine. CNC Toolholders come in various styles and specifications, tailored to different tools and applications. Some common types of toolholders include Endmill Extensions, Driven and Static Toolholders, and Boring Bar Sleeves for CNC machines. And don't forget the Morse Taper Drill Sockets. These tools ensure a stable connection between the tool and the machine spindle, allowing for precise and efficient machining.
Collets and Collet Chucks
Collet: A clamping device that holds cutting tools, such as end mills and drills, in a CNC machine. Collets provide uniform and secure grip, maintaining precise tool alignment during machining. Collets are sometimes called Collet Chucks, though there is a slight difference between the two tools. Overall, Collets come in various sizes and styles to accommodate different tool shank diameters.
Chucks
Chuck: A mechanical device that holds workpieces or tooling in CNC machines. Straight Shank Collet Chucks can be either manual or power-operated and come in various configurations, such as 2-jaw, 3-jaw, 4-jaw, or magnetic chucks. They ensure secure and accurate positioning during machining operations.
Workholding
Vises
Vise: A workholding device used to clamp and secure workpieces in CNC machines. Vises provide precise and rigid holding, enabling accurate and consistent machining. They come in different styles and sizes, such as milling vises, drill press vises, and sine vises, tailored to specific applications.
Clamps
Clamp: A fastening device used to secure workpieces on the machine table during CNC machining. Clamps provide adjustable and versatile holding solutions, ensuring proper workpiece stability and positioning. They are available in different types such as T-slot clamps, strap clamps, and toggle clamps.
Machining Tools
End Mills
End Mill: A CNC End Mill is a cutting tool used in CNC milling machines to shape and remove material from workpieces. CNC Endmills come in different grades, such as high performance endmills, and standard endmills for CNC machines, both have flutes (cutting edges) along their periphery and come in various designs to accommodate various milling operations, such as slotting, profiling, and contouring.
Drills
Drill: CNC Drills are rotary cutting tools used to create holes in CNC work products. High performance CNC drills and standard CNC drills both have helical flutes that evacuate chips from the hole and a pointed tip to facilitate cutting. They come in different types, such as twist drills, step drills, and split-point drills, to cater to specific hole-making requirements.
Taps
Tap: A cutting tool used to create internal threads in CNC machines. Taps come in different types, such as hand taps, machine taps, and spiral point taps, to accommodate various thread sizes and materials. They have sharp cutting edges that gradually cut threads into the hole as they rotate.
Programming
G-Code
G-Code: A programming language used to control CNC machines. G-Codes consist of a series of commands and parameters that direct the machine to perform specific operations, such as moving along axes, changing tool settings, and controlling spindle speed. They are standardized across different CNC machines.
CAM (Computer-Aided Manufacturing)
CAM: The use of computer software to generate toolpaths and other instructions for CNC machines. CAM programs take a CAD (Computer-Aided Design) model and use it to create a series of G-Code instructions that guide the machining process. CAM software allows for efficient and accurate programming, reducing human error and increasing productivity.
CNC technology has greatly transformed manufacturing processes, making them faster, more precise, and more efficient than traditional manual tools. Understanding the terminology related to CNC machines, tools, workholding, and programming is crucial for anyone working in the industry.
Looking for CNC tools and parts? You've come to the right place.
CNC Supply Solutions has the biggest selection of CNC machine parts, tools, toolholders, and accessories for every type of CNC application. We carry all the biggest brands like Dasqua, Haas, Global CNC, Mastercut, and more! Shop our huge selection of CNC parts and tools and find out for yourself why CNC Supply Solutions is the top CNC parts distributor online!